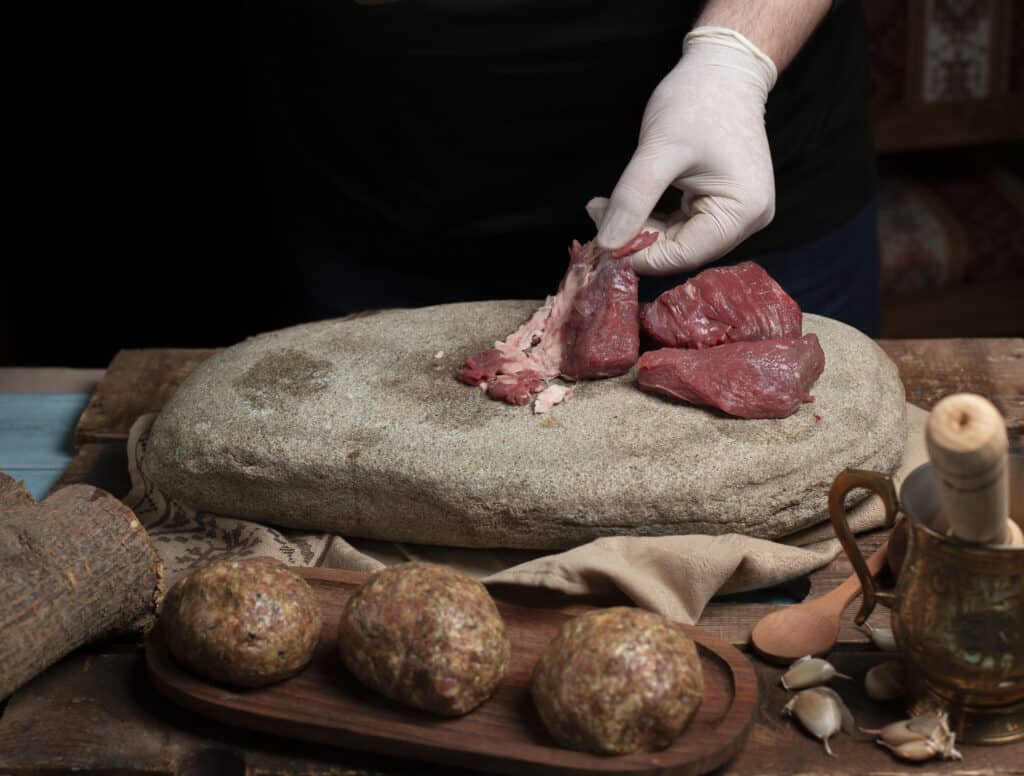
At the second annual Cellular Agriculture Innovation Day hosted by Tufts University, experts from various fields, including researchers, investors, and founders, gathered to discuss the future of cultivated meat. The event focused on the significant challenges in scaling and infrastructure that this emerging industry faces.
Yossi Quint, the founder and CEO of Ark Biotech, a bioreactor production company, shed light on the current state of cultivated meat infrastructure. He compared the output of one of the world’s largest cell culture facilities, Samsung Biologics in South Korea, to a typical Tyson facility.
Quint revealed that even if Samsung Biologics operated continuously for a year, its production of cultivated meat would still be less than what Tyson produces in a single day. To match Tyson’s output, Samsung Biologics would need to increase its production by approximately 10,000 times.
This staggering increase necessitates significant advancements in infrastructure, including larger bioreactors, more accessible cell media, and optimised filtration systems. Quint emphasised the need for a complete overhaul in infrastructure rather than incremental changes, suggesting that automation will play a crucial role due to the current lack of a sufficiently trained workforce.
However, scaling infrastructure for whole-cut cultivated meat presents unique challenges. Ryan Silvia, program manager of cultured meat scaffolding R&D at MilliporeSigma, explained that producing whole-cut meats involves using scaffolding material to support cell growth and vascularisation.
Each bioreactor, integrated with edible scaffolds, is used to produce a single unit of whole-cut meat. Given the single-use nature of these bioreactors and biological limitations on the size of whole-cut meats, scaling up is not a practical solution for this segment of the industry.
Silvia noted that no company is currently aiming to produce large-scale whole-cut meats, indicating a shift towards a ‘scale-out’ rather than ‘scale-up’ approach for this type of product.
Panellists also discussed more immediate solutions to these challenges. Shared infrastructure and pilot-scale manufacturing were highlighted as potential methods to enhance companies’ capabilities while reducing the initial capital required.
Lily Fitzgerald, senior manager of advanced technology programs at Massachusetts Technology Collaborative, suggested that communal sharing models, especially at the pilot scale, could mitigate the risks associated with developing specific types of infrastructure.
The insights from Tufts University’s Cellular Agriculture Innovation Day highlight the complexities and innovative approaches required to scale cultivated meat production. As the industry evolves, these discussions will be crucial in shaping its future and addressing the challenges it faces.